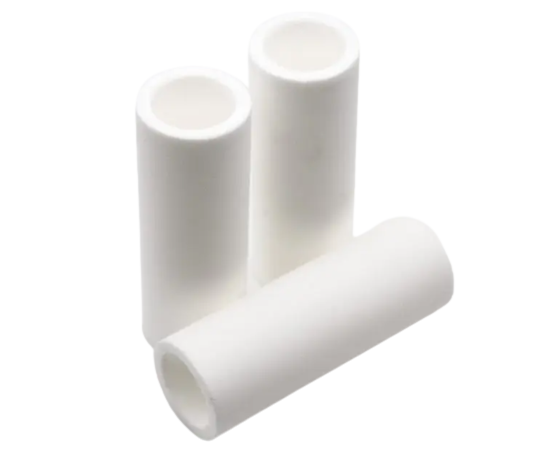
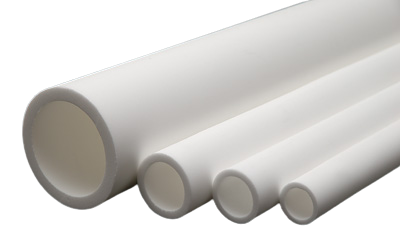
Porous plastic filters are specialized filtration devices designed to separate solids and liquids, or gases and liquids, by employing a porous material with precise and controlled pore sizes. These filters are used in various industries, including healthcare, industrial processes, environmental applications, and more, to remove contaminants, particulate matter, and impurities from fluids or gases. Here is a detailed introduction to porous plastic filters:
- Construction and Material:Porous plastic filters are typically made from high-quality polymers, such as polyethylene (PE), polypropylene (PP), or other thermoplastic materials. These materials are chosen for their chemical resistance, durability, and ability to maintain the desired pore structure. The manufacturing process involves sintering or extruding the plastic to create a matrix of interconnected pores, resulting in a highly permeable structure.
- Pore Size Control:One of the key features of porous plastic filters is the precise control over pore size. Manufacturers can tailor the filter’s porosity by adjusting parameters during production, allowing for customization to meet specific filtration requirements. Pore sizes can range from sub-micron levels to larger openings, depending on the application.
- Filtration Applications:Porous plastic filters are used in a wide range of applications, including:
- Medical Devices: In medical and life sciences, they are used in devices like IV filters, ventilators, and diagnostic equipment to ensure sterility and prevent contamination.
- Environmental Protection: These filters are used in water and air purification systems to remove impurities, bacteria, and particulates.
- Chemical and Petrochemical Industry: Porous plastic filters are employed to separate solids from liquids and gases in various chemical processes.
- Food and Beverage Industry: They help in the filtration of beverages, oils, and other consumable products to improve product quality.
- Aerospace and Automotive: Porous plastic filters are used in fuel and hydraulic systems to prevent contamination and maintain system integrity.
- Chemical Compatibility: The choice of polymer material for porous plastic filters is crucial, as it should be chemically compatible with the substances it will encounter. Different polymers offer various levels of resistance to acids, bases, solvents, and other chemicals, making it possible to use these filters in diverse environments.
- Temperature and Pressure Tolerance:Porous plastic filters are engineered to withstand a range of temperatures and pressures, depending on the application. They can function effectively in both low and high-temperature environments, making them versatile in various industries.
- Regenerable and Disposable Filters:Depending on the application, porous plastic filters can be either regenerable or disposable. Regenerable filters can be cleaned and reused multiple times, while disposable filters are discarded after use, ensuring convenience and cost-effectiveness.
- Maintenance and Lifespan:Regular maintenance and cleaning may be necessary for some porous plastic filters to ensure optimal performance and extend their lifespan. The lifespan of these filters depends on factors like the level of contamination and the operating conditions.
In conclusion, porous plastic filters are versatile and highly customizable filtration solutions used across numerous industries to maintain product quality, protect equipment, and ensure the purity of fluids or gases. Their ability to precisely control pore size and their chemical and temperature resistance make them valuable tools in a wide range of filtration applications.